Bike tech powers world record win
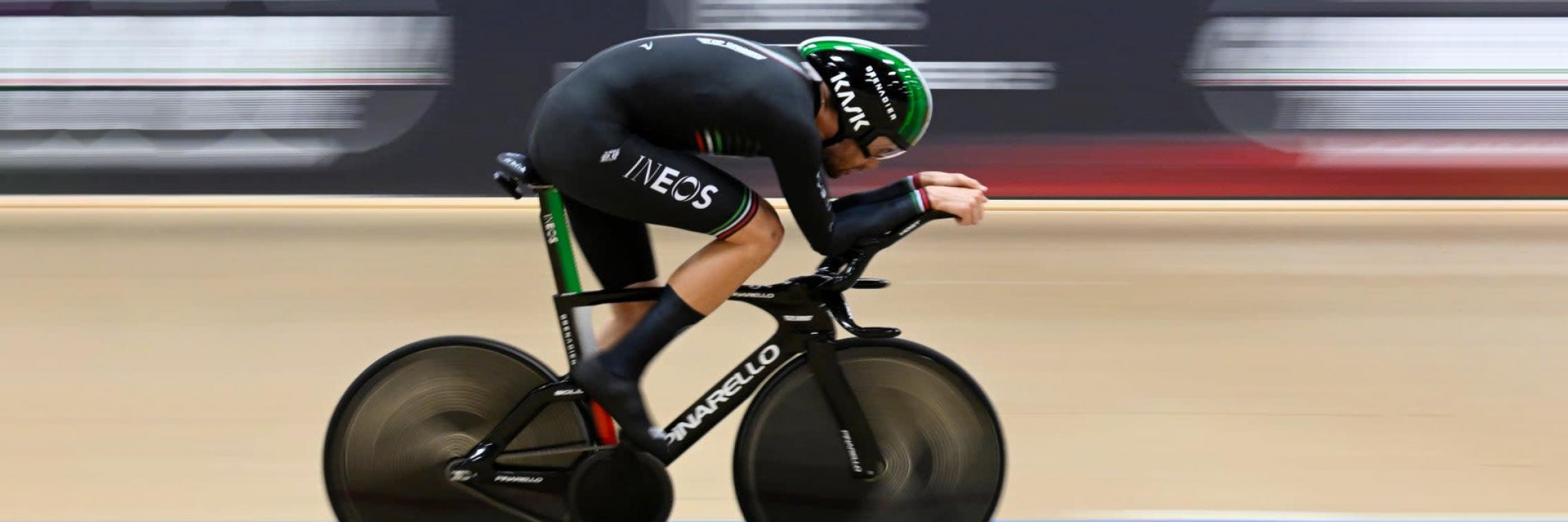
Humpback whales might not be the first creature that springs to mind when you think of aerodynamics – nevertheless, their incredible ability to make tight turns and spectacular leaps has inspired cutting-edge cycling technology that powered Olympic cycling champion Filippo Ganna hour world record win.
On October 8th in Grenchen Switzerland, the 26-year-old Italian cyclist broke the Union Cycliste Internationale Hour record, in which riders see how far they can cycle on an empty velodrome track in 60 minutes. Ganna registered 56.792 kilometres taking out the top spot, but to break this record the world class athlete will require a world class bicycle. The Italian manufacturer Pinarello has designed a 3D-printed bike specifically for this feat, which employs some truly cutting-edge technology.
There’s a critical design element on the Pinarello Bollide F HR 3D bike that could easily go unnoticed, but it’s essential for reducing air drag and increasing the top speed of the bike – and it was developed right here at the University of Adelaide.
Through many years of study into low-drag cycling equipment, researchers from the University of Adelaide’s School of Mechanical Engineering have developed tiny, precisely placed ridges called “tubercles” that work by directing air flow into regular vortices around the seat post to reduce drag. These tubercles were inspired by the ridges found on the fins of whales, which allow them to perform tight manoeuvres in the ocean.
“Reducing the drag on the bicycle frame in an area of high turbulence means the rider can travel further and faster for the same effort, which is crucial when attempting world records like this one,” said Associate Professor Richard Kelso, who is the co-developer of the tubercle-frame technology.
The tiny ridges may be effective, but they can also be extremely difficult to manufacture due to their size.
“Engineers at Pinarello and their UK partner Metron Additive Engineering have solved this problem by using cutting-edge 3D printing technology and a new high-strength alloy to produce the optimized tubercle shapes.”
What’s next?
Technological advancements are critical as our athletes push the limits of what is physically possible. With strong industry partnerships such as that between Pinarello and University of Adelaide engineers, the technological advancements made in our labs can be applied directly in the field.
“Innovation is at the core of Pinarello's bicycle designs, so it's great to be able to collaborate with them to commercialise our technology,” said Associate Professor Kelso.