Catalyst for more efficient chemical production on the horizon

Image: iStock.
An innovative technique is being developed by scientists that could allow Australia to lead the way in more sustainable manufacturing of fuels and chemicals.
“We have developed new synthesizing approaches that enable 3D printing techniques to be employed to automatically and efficiently produce customised, single-atom catalysts (SACs),” said the University of Adelaide’s Professor Shizhang Qiao, Director, Centre for Materials in Energy and Catalysis who leads the team.
“SACs can be tailored across a broad range of industrial applications.
“Our innovative technique has the potential to be more cost-effective and simpler than current approaches.”
The components of several precursors, including the affordable natural polymers and transition metal precursors, were mixed to form the printing ink. Afterwards, the ‘scaffold’ was printed directly by a 3D-printer. After the calcination and subsequent post-treatments, the isolated individual atom sites anchored on carbon supports were achieved.
To test the method, the team developed a new group of tailored catalysts with the aim of converting nitrate ions in wastewater to ammonia. Ammonia is one of the most fundamental chemical feedstocks in the world, as it is an indispensable chemical for fertilizer, pharmaceuticals and dyes. It is also considered an important way of storing energy and a carbon-free energy carrier. As one of the world’s most widespread water pollutants, nitrate ions converted by using catalysts are transformed into a nitrogen source.
“By simplifying the way catalysts are manufactured, this new technique has the potential to advance Australia’s status as a global leader in tackling the effects of climate change and help us take the lead in new techniques for making chemicals that benefit society.”The University of Adelaide’s Professor Shizhang Qiao, Director, Centre for Materials in Energy and Catalysis.
“SACs are promising candidates for the next generation of highly efficient catalysts however directly synthesizing SACs is still challenging and expensive,” said Professor Qiao.
“Our synthesizing approach allows 3D printing technique to be employed as a promising avenue to manufacture of SACs at different scales, paving the way for using them to achieve sustainable production of valuable fuels and chemicals.
“By simplifying the way catalysts are manufactured, this new technique has the potential to advance Australia’s status as a global leader in tackling the effects of climate change and help us take the lead in new techniques for making chemicals that benefit society.”
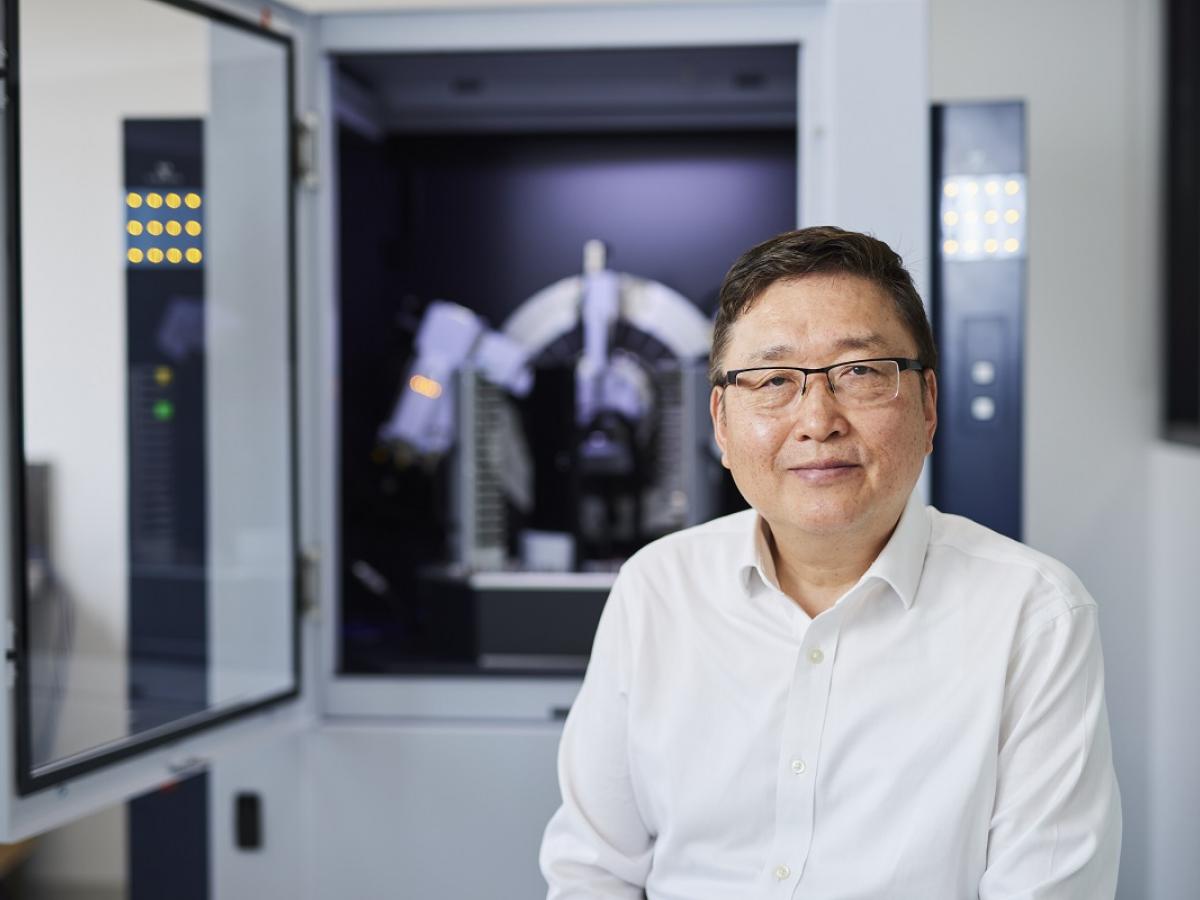
The University of Adelaide’s Professor Shizhang Qiao, Director, Centre for Materials in Energy and Catalysis.
The team published their findings in the journal Nature Synthesis.
“Our team will further explore the potential of 3D-printed single-atom catalysts in various applications, such as catalysis in other chemical reactions which are critical in chemical engineering industry,” said Professor Qiao.
The team’s work will inspire the development of a new generation of advanced catalysts. This new avenue of research is expected to accelerate the development of single-atom catalysts and make them technically and economically available for the chemical engineering industry within 10 years.
Media contacts
Professor Shizhang Qiao, Chair of Nanotechnology, Director, Centre for Materials in Energy and Catalysis, School of Chemical Engineering and Advanced Materials, The University of Adelaide.
Mobile: +61(8)8313 6443, Email: s.qiao@adelaide.edu.au
Jessica Stanley, Media Officer, University of Adelaide.
Mobile: +61(0)422 406 351, Email: Jessica.stanley@adelaide.edu.au